Call us now:
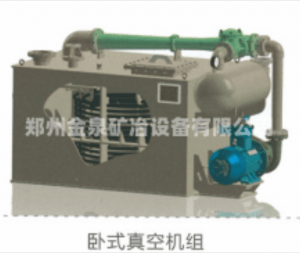
Vacuum unit equipment
I. Equipment Features The vacuum unit is composed of a series of units including anti-corrosion PP water tank, buffer tank, RPP water jet pump, check valve, steam-water jet pump, and
Extraction of precious metals from copper anode mud
The chemical process of extracting precious metals from copper
anode mud first converts the precious metals in the copper anode mud
into water-soluble sulfates through sulfuric acid roasting, then evaporates
and recovers selenium, and then uses dilute acid to leach copper to dissolve
it in the liquid to form copper sulfate.
Sodium chloride is then added to form silver chloride precipitation,
and sodium sulfite is reduced to recover silver. Then gold is reduced and
precipitated into gold powder after forming AuCl₄⁻ in a chlorine-containing
solution.
The platinum and palladium removed from acid leaching are reduced,
dissolved, oxidized, and hydrolyzed, and then precipitated with ammonium
chloride to obtain sponge platinum and sponge palladium.
Firstly, the process requires using a rotary furnace or a fluidized bed
roaster to sulphate roast the anode mud; additionally, the system must be
equipped with a selenium evaporation recovery device to efficiently capture
selenium.
Next, leaching reactors and mixing tanks made of acid-resistant materials
are deployed, thereby ensuring that the aggressive chemical environment is safely
managed.
Furthermore, filters or centrifuges are utilized for effective solid–liquid
separation, and subsequently, special sedimentation tanks and reduction reactors
are installed to precipitate and reduce the targeted metals. Moreover, delivery
pumps, pipelines, and liquid storage tanks are incorporated into the design to
guarantee continuous and controlled fluid movement.
Consequently, after thoroughly analyzing the raw materials and designing the
refining plan, the equipment can be systematically sorted and calculated, which
ultimately enhances process efficiency and reliability.
I. Equipment Features The vacuum unit is composed of a series of units including anti-corrosion PP water tank, buffer tank, RPP water jet pump, check valve, steam-water jet pump, and
Jinquan Electrochemical Deposition Equipment The electrochemical deposition system has revolutionized traditional metallurgical processes through dynamic flow field control technology and is widely used in
Intelligent gold electrolysis equipment combines automatic control, intelligent monitoring and efficient electrolysis technology. It can process raw gold materials with a purity of more than
Jinquan Electrolysis - Cyclone Electrowinning Equipment Cyclone electrowinning equipment is widely used in gold plating solution, gold stripping solution, gold ore heap leaching, spraying solution