Call us now:
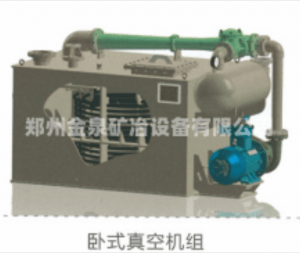
Vacuum unit equipment
I. Equipment Features The vacuum unit is composed of a series of units including anti-corrosion PP water tank, buffer tank, RPP water jet pump, check valve, steam-water jet pump, and
Loaded catalysts for platinum and palladium recovery
Various types of supported catalysts enjoy wide use in the chemical and petrochemical
industries. For example, they enable hydrogen peroxide production via the anthraquinone method,
synthesize urea, remove CO from ammonia synthesis raw gas, and hydrogenate benzene to
produce cyclohexane. In addition, these catalysts support catalytic combustion of low-concentration
organic volatiles and heavy oil refining. They also facilitate reactions such as isomerization, cracking,
hydrogenation, and dehydrogenation.Loaded catalysts for platinum and palladium recovery
Among various carriers, Al₂O₃ predominates, while smaller amounts of SiO₂ and CaCO₃ carriers find
application. Typically, manufacturers use platinum and palladium to form two catalyst series: Pt/Al₂O₃
and Pd/Al₂O₃. Depending on the specific purpose, catalyst compositions incorporate 0.01–0.5% platinum
and palladium, which classify them as low-grade waste. Moreover, spent Al₂O₃ catalysts appear mainly
as 3–5 mm spheres or cylinders. Notably, the carrier’s crystal structure splits into a-type and y-type;
the a-type remains insoluble in acid, whereas the y-type dissolves readily.
Catalyst Regeneration and Recovery Techniques
The key to regeneration and recovery lies in effectively separating platinum or palladium from the carrier to yield enriched or refined metals. For example, one method stirs (or percolates, soaks) the catalyst with acid or other chemical reagents to leach out platinum and palladium. Subsequently, processes such as anion exchange, zinc (or iron, aluminum) replacement, activated carbon adsorption, sodium sulfide precipitation, and xanthate precipitation further enrich the solution. Alternatively, leaching the carrier first produces a residue enriched in platinum and palladium. After either extraction method isolates the crude metals, further refining into pure metals poses no technical challenges.
Supported catalysts prove essential in numerous industrial applications. Manufacturers optimize catalyst performance by carefully selecting carriers and adjusting precious metal contents. Furthermore, recovery technologies demonstrate that active separation and targeted leaching efficiently retrieve platinum and palladium, paving the way for refining them into high-purity metals.
Loaded catalysts for platinum and palladium recovery
I. Equipment Features The vacuum unit is composed of a series of units including anti-corrosion PP water tank, buffer tank, RPP water jet pump, check valve, steam-water jet pump, and
Jinquan Electrochemical Deposition Equipment The electrochemical deposition system has revolutionized traditional metallurgical processes through dynamic flow field control technology and is widely used in
Intelligent gold electrolysis equipment combines automatic control, intelligent monitoring and efficient electrolysis technology. It can process raw gold materials with a purity of more than
Jinquan Electrolysis - Cyclone Electrowinning Equipment Cyclone electrowinning equipment is widely used in gold plating solution, gold stripping solution, gold ore heap leaching, spraying solution