Call us now:
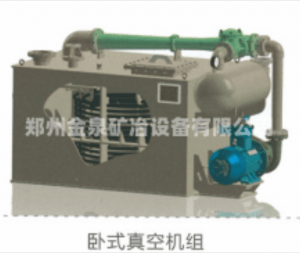
Vacuum unit equipment
I. Equipment Features The vacuum unit is composed of a series of units including anti-corrosion PP water tank, buffer tank, RPP water jet pump, check valve, steam-water jet pump, and
Process of smelting waste catalyst into palladium
1. Raw material pretreatment
(Dissolution and conversion: Waste catalyst needs to be smelted or
acid-leached to convert into chloropalladic acid (H₂PdCl₄) solution.
2. Oxidation and precipitation:
Reaction formula: Pd + 4HNO₃ + 6HCl → H₂PdCl₆ + 4NO₂↑ + 4H₂O
Step 1 – Oxidation:
Operators first pump chlorine gas or inject hydrogen peroxide into the
chloropalladic acid solution containing Pd²⁺, actively driving the oxidation
of Pd²⁺ to Pd⁴⁺.
Step 2 – Precipitation:
Subsequently, they add an excess of 10-15% ammonium chloride (NH₄Cl)
to the solution, triggering the formation of a deep red crystalline ammonium
chloropalladate ((NH₄)₂PdCl₆) precipitate. This reaction selectively traps
base metal impurities (e.g., Cu, Fe), enabling their physical separation via filtration.
Step 3 – Redox Cycling:
Next, the team boils the collected precipitate in a controlled reactor, reducing it
to soluble ammonium chloropalladate ((NH₄)₂PdCl₄). To further enhance purity,
they reoxidize the solution through additional chlorine gas exposure, completing
a redox purification cycle.
3. Ammonia complexation:
Heat the chloropalladic acid solution to 80°C, add ammonia water to adjust the pH
to 8-9, generate soluble dichlorotetraamminepalladium ([Pd(NH₃)₄]Cl₂), which can
separate the impurities. Therefore, this process requires multiple repetitions to achieve
purification.
4. Calcination-hydrogen reduction:
The calcination process decomposes the purified palladium salt into palladium oxide (PdO)
From waste to wealth: Through cutting-edge hydrometallurgy paired with smart reactors,
spent catalysts are transformed into 99.99% pure palladium. Key innovations include
(1) precision impurity removal via redox cycling;
(2) AI-controlled pH adjustment for ammonia complexation;
(3) energy-efficient hydrogen reduction. Together, these advancements slash processing
I. Equipment Features The vacuum unit is composed of a series of units including anti-corrosion PP water tank, buffer tank, RPP water jet pump, check valve, steam-water jet pump, and
Jinquan Electrochemical Deposition Equipment The electrochemical deposition system has revolutionized traditional metallurgical processes through dynamic flow field control technology and is widely used in
Intelligent gold electrolysis equipment combines automatic control, intelligent monitoring and efficient electrolysis technology. It can process raw gold materials with a purity of more than
Jinquan Electrolysis - Cyclone Electrowinning Equipment Cyclone electrowinning equipment is widely used in gold plating solution, gold stripping solution, gold ore heap leaching, spraying solution