Call us now:
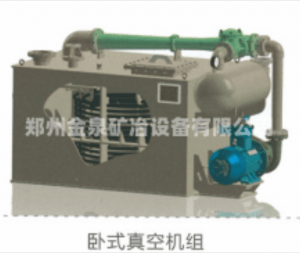
Vacuum unit equipment
I. Equipment Features The vacuum unit is composed of a series of units including anti-corrosion PP water tank, buffer tank, RPP water jet pump, check valve, steam-water jet pump, and
Recently, many customers at home and abroad have requested technical articles on refining spent three-way catalysts to recover platinum, palladium, and rhodium. In order to provide a wide range of answers, I have written this article.
From the perspective of environmental protection, directness, labor saving, and recovery rate, we recommend the use of smelting enrichment-hydrochloric acid iron removal-extraction separation-classic refining process. After nearly six years of experimental research and production implementation, this process has become a mature and reliable process. in:
1. The smelting and enrichment stage includes:
a): The waste three-way catalyst enrichment process is crushing-pulverizing-mixing-smelting-iron alloy block.
b): Slag refining-grinding and selection.
c): Secondary smelting by slag grinding-iron alloy block.
d): The trace dust produced by crushing and crushing is recovered by the cyclone dust collector.
e): The wastewater generated by grinding and gravity separation is recycled.
2. Hydrochloric acid iron removal process includes:
a): Iron alloy block - smelting again to remove slag - water crushing - iron alloy particles - pulverized to 120 mesh - hydrochloric acid reaction to remove iron - cooling, filtering and washing - precious metal slag.
b): Reaction wastewater treatment to recover ferrous chloride (grass green) for sale.
c): The generated wastewater is transported to the wastewater section for treatment through pipelines.
d): The generated hydrogen is recycled and used in the hydrogen reduction section to reduce rhodium.
3. Extraction and separation process includes:
a): Precious metal slag aqua regia liquid preparation - nitrate removal and filtration - filtrate adjustment to extract palladium - extraction residue filtering, oxidation and extraction of platinum - extraction residue hydrolyzed to precipitate rhodium.
b): The washing water and regenerated water with high impurity content produced after repeated accumulation and use contain a small amount of platinum, palladium, and rhodium. The platinum and palladium are extracted and the rhodium is recovered through zinc replacement.
c): The oil-free wastewater generated during the process is transported to the wastewater section for treatment through pipelines. The oily (trace) wastewater is separated by the oil-water separator and then passed through ozone to digest the oil smell, and then piped to the wastewater section for treatment.
d): The oil smell generated during the extraction is collected and frozen through the gas collecting hood and the oil is collected. The tail gas after the oil collection is decomposed by ozone and transported to the exhaust gas section for treatment through pipelines.
4. Classic refining techniques include:
a): Palladium stripping solution purification - reduction washing - absolute ethanol washing - drying and selling (or selling as ingots) with a palladium content greater than 99.99%;
b): Purification of platinum stripping solution - hydrochloric acid acidification - oxidative hydrolysis - ammonium chloride precipitation - calcination - ingot sale with platinum content greater than 99.99%;
c): liquid preparation of rhodium precipitation residue - reduction hydrolysis - acidification of hydrolyzate - rhodium precipitant to precipitate rhodium - rhodium complex is calcined into rhodium oxide - hydrogen reduction, the content is greater than 99.95%;
d): Any tail gas generated during the process is frozen to recover the acid mist (recycled for use) in the highly integrated reactors, hydrolysis machines, and suction filters of each section, and then processed by the respective atomization exchange systems before being transported to the tail gas treatment by the main pipe. Processing and emptying of the work section;
e): Any wastewater generated during the process will be transported to the wastewater section for treatment through pipelines after being tracked and tested to be free of platinum, palladium and rhodium.
I. Equipment Features The vacuum unit is composed of a series of units including anti-corrosion PP water tank, buffer tank, RPP water jet pump, check valve, steam-water jet pump, and
Jinquan Electrochemical Deposition Equipment The electrochemical deposition system has revolutionized traditional metallurgical processes through dynamic flow field control technology and is widely used in
Intelligent gold electrolysis equipment combines automatic control, intelligent monitoring and efficient electrolysis technology. It can process raw gold materials with a purity of more than
Jinquan Electrolysis - Cyclone Electrowinning Equipment Cyclone electrowinning equipment is widely used in gold plating solution, gold stripping solution, gold ore heap leaching, spraying solution